品牌君航
是否加工是的
种类二辊轧机、三辊轧机、四辊轧机、六辊轧机
轧辊辊套材料YG8\YG15
重量按工艺设计
轧辊直径75-350
功率3KW-120KW
调速方式汇川变频
轧制精度±0.005mm
轧制速度0-90米/分钟
焦作君航机电科技有限公司位于华夏文明发祥地河南•焦作**产业开发区,公司主要生产:线材精密主动四辊轧机、精密两辊轧机、异型线材轧机、辊模双驱牵引拉拔机、校直机、空芯卷精密绕线机、工字轮精密绕线机、H型钢焊丝放线架等非标线材设备以及线材配件。
如何处理轧机应用中的具体问题?
目前,在带钢加工过程中,新的轧机设备是必不可少的组成部分。它的压路机可以提高钢带的主题活动性和冷轧辊的平整度,进而提高轧辊的使用效率,从而提高轧辊的使用寿命。但在具体应用中,压路机设备一般都装有恶性渗油和堵管补偿油。其机械配备目前,常见故障的原因与实际操作的基本原理紧密结合起来掌握。
由于轧辊径向连接的实际操作,根据轧辊的实际操作产生钢连接头进行维护,位置传感器安装在收卷辊上,准确测量出轧辊左右的实际操作情况,可以改善带钢的外观,当需要控制弯辊时,液压传动系统改变轧辊的工作压力,使正拉应变和正压强度的弯辊部分释放到实际工作辊和轧机的车削槽中,改变控制器的保持方式。
在移动电机轴的拆卸显示信息中,弯曲杆上的支承点环和滚柱的轴承端盖损坏严重,且厚度较薄,故对运行中的径向力进行冷轧方位钻孔,并与工作压力滚柱一起施加承受冷轧方位角时,径向切削速度对液压缸的损伤很大,根据现场应用发现,传动系统侧的连接缸为燕尾槽,与滚柱轴承座一起使用,使弯曲的发动机缸能减小使用工作压力辊时,径向钻削并释放较大的径向切削速度,在实际操作侧会降低弯辊的使用寿命。
当轧机辊不在零位时,机器设备侧面的锁不打开,机器设备不到位。在初步设计方案中,利用自动开关检查模块侧面的连接辊。由于更换辊和水蒸气的实际作用,自动开关基本上不可能检查辊的变化,由于自然环境和时间的限制,在运行过程中经常会因为辊在模块侧没有堵塞而产生。

轧辊轴承的安装与处理
轧辊轴承的储存保管
轴承内外圈组件要用塑料包裹,轴承的包装设计应满足轴承的防潮和防尘要求。为防止内外圈发生椭圆变形,应保持轧辊轴承水平放置,应将轴承储存在原包装箱内,并放在枯燥的场所。在尘埃,湿润环境中,不允许将轴承从包装中移出并放置在托盘上或敞开式货架上。所有的轴承安装部件应该清洁并处于良好状况,应该保持作业台、安装区清洁,不能在焊接区和机械加工设备旁安装轴承部件,防止碎屑和污物进入轴承。
轧辊轴承使用前后的处理
新轧辊运进厂时注意防止磕碰,经过检查及有关部门同意后,使用前对新轧辊编号,按照顺序安装,在头端装上轴承内套和密封端盖等零件。
通用的安装方法:将轴承内套用油或电加热器加热到%~200%,当内套胀大后趁热装到轧辊辊颈上。为了延迟疲劳损伤,防止作业中发生各种故障事端,就应及时查看,恰当保养。形成制度化,**轴承在使用期内,运转良好。
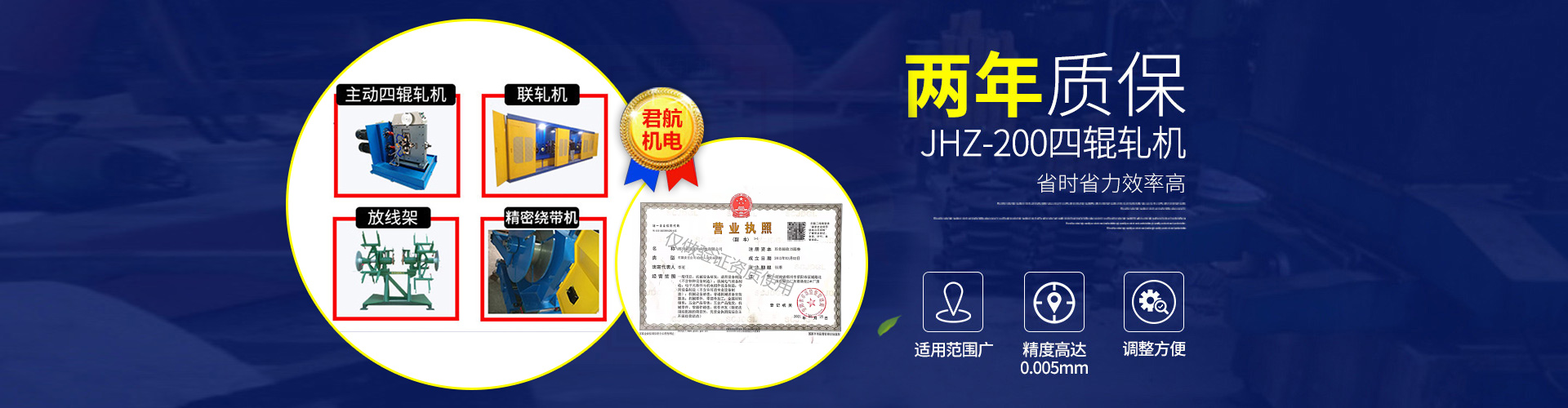
精密轧机轴承故障发生的原因
1、装配原因
轴承器械非常精密,装配工作需要非常严谨,如若装配过程疏忽,则有可能导致轴承座或压辊的装配区间发生偏移, 导致滚动圆柱进入轴承座时发生过磨,内滑道受损,运转时产生噪音或振动的情况。同时,装配不良也有可能导致轧机
两侧辊缝高度相差**过正常值,这将导致错辊的情况发生。同时,在装配过程中由于用力大小不一,轴承游隙产生变化, 继而使得轴承平均受力范围不均衡,致使轴承的抗磨系数降低,继而导致轴承故障率攀升,从而影响正常的职能工作效率降低轴承使用寿命。同时,轧机在装配过程中由于承载的压力有一定的限度,**过限度或轧机电流过载等造成的轧机压制压力突变导致的轴承负荷变化,也会导致轧机轴承在运转过程中出现故障。在实际生产过程中,有些企业片面追求生产效益,缺乏对设备装配过程中重要注意点的准确把握, 轴承元件的不契合,会强行轧制,造成轧制变形,这样在轴承实际运作过程中,就会造成局部压力过大导致轴承运转载荷受到冲击,损坏轴承 。
2、润滑系统故障
轧机轴承在运转的过程中需要保证有足够的润滑剂**其润滑,若润滑系统出现故障,造成润滑剂不足,则会导致轴承异响的发生。通常情况下,轧机的润滑系统在正常工作之前,首先要做一次全面的清理和排查,**整个系统的干净、清洁,**轴承中没有粉尘颗粒和其他杂质污物的侵蚀, **轴承运作过程中整个油路的畅通无阻,**润滑系统的正常运行,如做不到这一点,则有可能导致润滑系统的实效, 从而引发轴承故障。
3、人为原因
在轧机轴承故障中,人为因素也不容忽视。有些故障若人力及时清查、谨慎操作,完全可以避免,但却因为操作或排查人员的大意、不谨慎,而造成了轴承或相关联设备元件的故障。其根本原因在于工作人员工作不严谨,在需要认真看护并经常检修的发电设备中未能及时进行维护和保养, 在使用过程中不注意操作规程,对于轧机的具体操作规程了解不详细全面就开始实际操作,因而在实际生产的过程中导致轧机轴承的故障率上升,影响到正常的生产。
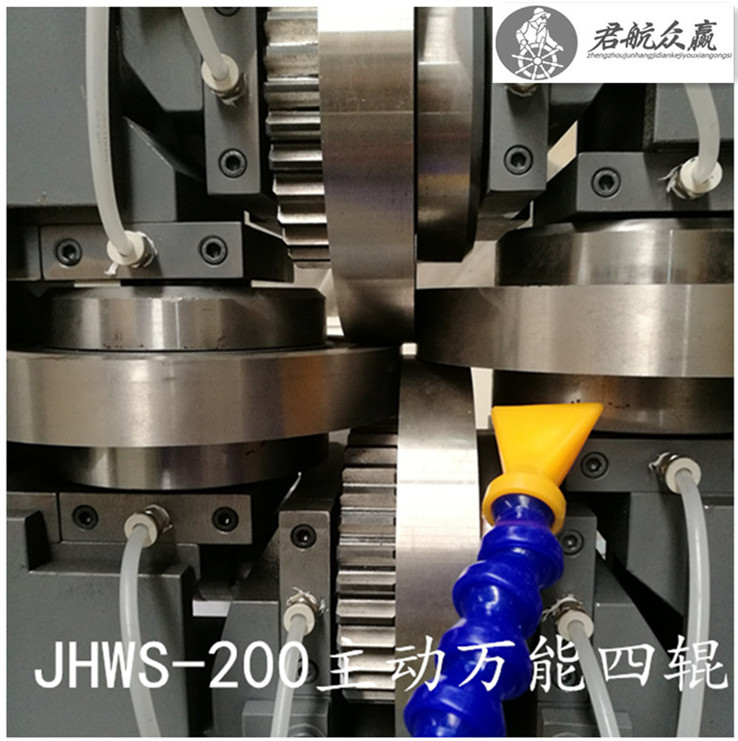
精密轧机轴承故障的防范对策
1、轴承装配过程中的防范对策
轴承的安装一般分为压入安装和热装两个部分,压入安装一般利用压力机或者人力进行,由于装配技法不到位可能造成轴承轴辊等部位受损,因而在安装时要注意安装力度, 比如四列圆锥滚子轴承的安装过程中,需要首先将轴承步入轴承箱,然后再将轴承箱植入轴颈中。四列圆锥滚子轴承外圈与轴承箱孔亦采用动配合,先将外圈 A 装入轴承箱。同时保证出厂时轴承内外圈以及隔圈都印有字符符号,保证装入曲轴箱的次序,防止轴承游隙的改变。
热装环节一般针对大型轴承而言,由于一般的机械很难产生巨大的推力将轴承压入大型轧机中,因而采用在油中将轴承加热,使其膨胀之后再装入轴上。在使用这种方法时要注意轴承加热的温度一般为 100℃,装配时需要将轴承吊起来进行,安装完毕后还要避免轴承的热胀冷缩对使用的影响,使用轴螺母使之紧固。
2、检查轴承
为了保证轴承装配的质量,需要对轴承进行检查,该检查过程分为装配前的检查、运行中的检查、静止状态的检查、拆后检查等多个环节。
1)在轴承装配前需要对轴承各部分的规格和尺寸进行严格检查,按照相应轧机的正确装配过程对其进行良好的装配, 务必要核对重点器件的尺寸,比如要保证轴承游隙和定位轴承游隙在合理安全的范围内。
2)在运行过程中,也需要通过的听检设备,对运行中的轴承进行听检,这一检查过程重点对轴承内部运作情况进行检视,需要使用的检测仪进行,提前预防潜在故障的发生。
3)在轴承运转停止后,要及时对轴承相关部件进行检查, 对轴承关键部位有无松动进行检测,以防止污染物对轴承本体的污染,造成轴承过度运转以及损坏。在静止检查过程中, 需要对损伤的轴承进行更换,以免造成更为严重的机械损伤, 使得轴承面临更大风险。
4)轴承安装完毕后,还要对轴承进行进一步的安装校验, 确保其安装不存在纰漏。具体的校验步骤为工人用手旋转轴承,进行听检校验,检查是否存在压痕异响或异物异响。排除压痕异响和异物异响之后,还需要进行动力运转检验,检验在没有负荷作用到有负荷作用,并在慢慢提速的过程中, 是否会存在润滑油泄露的情况,如果出现问题应该及时进行检修。
以上轴承检查环节基本做到了对不同运行状态下轴承健康状况的全面掌握,通过检查也可看出轧机轴承的故障多发且在实际检修过程中存在较大的安全疏漏,只有更加全面细致地完善轧机轴承的检修与保养,才能保证轧机在实际使用过程中尽可能少出现故障。
焦作君航机电科技有限公司历经数年努力,不断创新,所研制生产的不锈钢三角丝精密四辊四联轧、矩形弹簧钢丝五联轧、异型线材四联轧、矩型线三联轧+牵引等设备受到国内外客户高度认可。欢迎广大客户来电咨询!
http://zzyh0371.cn.b2b168.com